Steel research in space: Tata Steel Nederland and ESA join forces
by David Fleschen
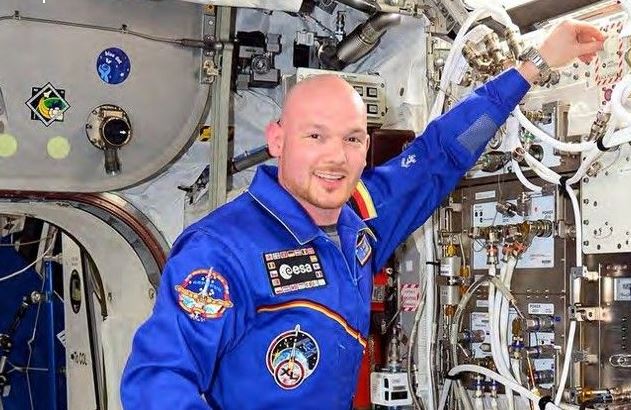
The European Space Agency (ESA) and Tata Steel Nederland (TSN) have embarked on a groundbreaking project to conduct steel research aboard the International Space Station (ISS). This unique collaboration, under the "Space for Science" program, aims to explore the thermo-physical properties of steel during casting, contributing to advancements in energy efficiency, sustainable production, and the global green transition.
Innovative experiments on the ISS
Currently, research is underway on steel designed for electric motors, which are pivotal to the efficiency of technologies like electric vehicles. Understanding the complex structures that form during the casting process allows scientists to enhance steel quality, minimize production errors, and optimize materials for energy-efficient applications.
Tata Steel Nederland provides meticulously prepared steel samples and expertise, while ESA manages the experimental processes on the ISS. The steel samples undergo a series of controlled cycles of melting and solidification in the state-of-the-art Electromagnetic Levitator (EML). This container-free environment in microgravity eliminates disturbances caused by gravity, enabling precise measurements and purer data collection.
Dr. Begona Santillana, a researcher from Tata Steel’s R&D department and the project’s initiator, explains the significance of conducting experiments in space: “The transition from liquid to solid steel is a critical phase where much can go wrong. In the microgravity environment of space, we can obtain highly accurate data without the influence of Earth’s gravity, providing insights into properties like viscosity, surface tension, and electrical conductivity.”
The Electromagnetic Levitator: A key tool
The EML, first activated aboard the ISS in 2014, is a sophisticated facility that uses electromagnetic fields to levitate and process metal samples without physical contact. The absence of container walls during these experiments ensures unparalleled measurement accuracy. Over the past decade, the EML has facilitated over 500 days of research and processed 54 samples, yielding critical data for both scientific and industrial applications.
The knowledge gained from these experiments supports the production of high-quality steel with fewer process inefficiencies, leading to significant energy savings. Additionally, insights from the EML's research have broader applications, including materials for wind turbines, solar panels, and semiconductors—key components of sustainable energy solutions.
Source and Photo: Tata Steel Nederland