Supply Chain Management in Time of Corona - A Challenge
by Dagmar Dieterle
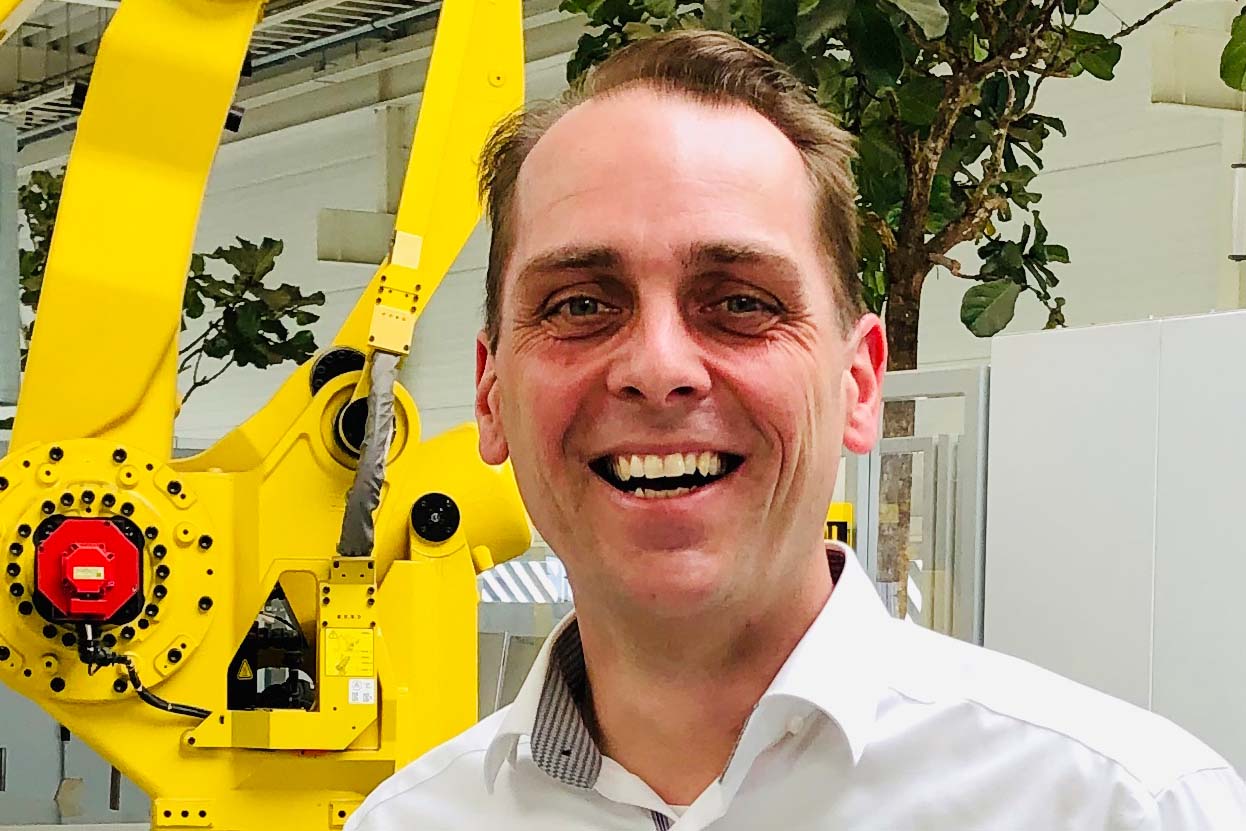
marketSTEEL interview with Frank Gelen, COO of 247TailorSteel
While the corona virus has turned the daily lives of employees of 247TailorSteel upside down, the company is still able to deliver ordered products on time. Customers can continue to order via the Sophia® online portal, giving them " direct access to the machinery" around the clock. With two independent production plants, in the Netherlands and Germany, 247TailorSteel can flexibly schedule its production capacity and therefore the risk of production breakdowns is low.
In the following interview with COO Frank Gelen you will find out how 247Tailorsteel deals with the coronavirus in daily operations, how it ensures the safety of its own factories and why the company is able to continue to serve its customers well.
marketSTEEL: What influence does corona have on supply chain management at 247TailorSteel?
Our company philosophy is based on a multi-sourcing strategy in our purchasing department. This means we are not dependent on just one supplier. We have agreements with our suppliers for larger volumes and can therefore ensure our daily order intake. With the order volume of 247TailorSteel we are a very important customer for our suppliers. This enables us to conclude framework agreements with our suppliers, which allows us to call off material flexibly.
marketSTEEL: How does 247TailorSteel manage security in the factory? Do you go an "extra mile"?
Just like many other companies, we have a daily crisis meeting (often with teleconferencing) and communicate the measures precisely to our employees. In both production plants (Netherlands and Germany) we have taken steps that go further than the official regulations. For example, we no longer have a handover at the change of shifts and therefore the employees have no direct contact when changing shifts. We have also established separate breaks, which also minimises the transmission of the virus. We also organise fitting rooms in phases.
marketSTEEL: How does the high degree of digitalization and automation benefit this corona situation?
As a result of our extensive automation, we have precise work preparation with only a few employees and the processes are automated. Just a few employees are still required and can carry out this process step from home. As a result, we have only a handful of employees in our building, so we can use them specifically and "virus-proof" in production. Our automation with the AGVs also avoids human interaction and therefore minimizes the chance of corona infection.
marketSTEEL: What are the biggest challenges in delivering products to customers on time? How does 247TailorSteel handle these challenges?
We see challenges in the transport sector. We organise most of our transport ourselves and therefore are able to deliver to our customers on time. However, we advise our employees to stay at home in case of any suspicious corona symptoms. The transport in Germany runs via various transhipment points, which can lead to delays in individual cases. In addition, personal contact is naturally a special challenge.
Besides the fact that we as a company take all precautions to prevent the spread of the virus, I hope that we can leave this corona situation behind us quickly and that we can all continue in good health.
More information: www.247TailorSteel.com
Photo: 247TailorSteel