A possible future of steelmaking: HIsarna
by David Fleschen
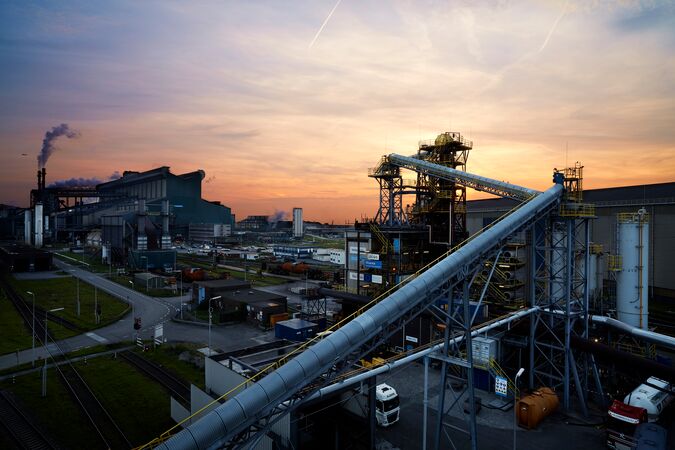
Reducing CO2 significantly and even being able to find ways of carbon neutral steel production. This is certainly one of the key challenges the steel industry is facing in the 21st century. One of the possible ways to produce steel in the future is the so called HIsarna technology, which is tested in a pilot plant on the Tata Steel in Europe ground in IJmuiden, the Netherlands.
MarketSteel was allowed to visit the plant as a part of a press tour and was able to see how well the technology does already work in practice. Indeed, even though first plans for a cyclone oven based technology existed in IJmuiden ever since the 1960s, HIsarna has made its most considerable progresses during the past years.
While the plant was constructed in 2010 and the first metal was produced in 2011, the test plant is now increasingly demonstrating its energy efficiency, while it also allows to include ever more materials, such as sustainable biomass and scrap, in the melting process.
“HIsarna is a breakthrough technology offering significant environmental and economic benefits”, explains Johan van Boggelen, operations manager of the HIsarna pilot plant. “It’s a revolutionary change of the ironmaking process, providing a large step improvement towards meeting the global environmental targets. In addition it offers economic advantages through process intensification, increased raw material flexibility and product quality.”
According to Tata Steel in Europe, HIsarna will be an enabler for a sustainable global steel industry. Figures are quite remarkable: According to Tata Steel, the test plant already demonstrated reduction of CO2 emissions by more than 50%, without carbon capture technology. With carbon capture and storage, even 80 % reduction of CO2 is possible. In addition the new technology does reduce fine dust emission, and is meant to be able to also reduce overall steelmaking costs in the long run.
Certainly the idea behind HIsarna is rather simple: Combining all smelting processes in a single cyclone oven, instead of having to separate coking and smelting as well as ore agglomeration in the form is sinter and pellet making, which is not required for HIsarna. But there is a lot of detail involved in every part of the melting process, as Johan van Boggelen explains: ”Iron ore is injected into the smelt cyclone, together with oxygen. Hot CO rich gas from the SRV is combusted in the smelt cyclone, increasing the temperature and causing the iron ore to melt and partly pre-reduce.
The molten and partly reduced iron ore will form a liquid film along the wall of the cyclone after which it drops down into the slag layer in the SRV. Granular coal is injected in the slag layer. This will fully reduce the iron ore to liquid hot metal and carburise the hot metal bath. The reduction reaction produces CO gas. This is partly combusted with oxygen in the space between the top of the slag and bottom of the cyclone, in order to generate heat. The splash and turbulence resulting from the injection processes ensure part of this heat is transported to the slag and metal bath.”
HIsarna is one of the four process developments that originate from the ULCOS project, a consortium of 48 European companies and organizations from 15 European countries that have launched a cooperative research & development initiative to enable strong reduction in CO2 emissions from steel production. Since 2007 Tata Steel, Rio Tinto and ULCOS have been put their efforts together and actively developed this coal-based smelting reduction process. ArcelorMittal, thyssenkrup, voestalpineand Paul Wurt are further partners of the project. In 2017, Tata Steel bought the intellectual property rights from Rio Tinto and now owns all HIsarna rights.
To date over 75 mlnEuro have been invested in the HIsarna technology, partly funded by the European Union’s Horizon 2020 research and innovation program.
photo: Tata Steel in Europe