ABB makes low-carbon copper commitment in metallurgy technologies
by David Fleschen
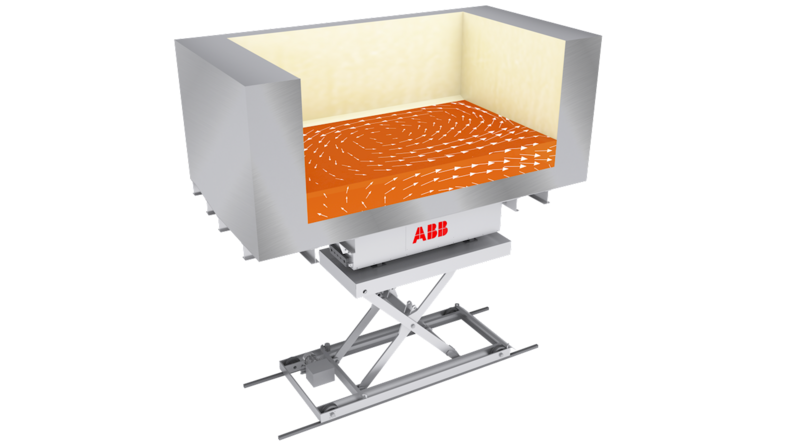
ABB will purchase low-carbon copper winding wire from global provider Dahrén for use in the manufacturing of its electromagnetic stirring (EMS) equipment. The commitment builds on similar supply chain connections for ABB stirrers used in the production of metals.
The supplier, which operates primarily in Sweden, Germany and Poland, receives raw copper mined by Swedish mining and smelting company Boliden using fossil-free energy and processes it into wire. Copper is a vital material for manufacturing industrial electrical equipment, but its production is energy intensive. The carbon footprint of the Boliden product used by Dahrén is known to be 65 percent lower than the industry average.
“We believe we are in a breakthrough year for low-carbon and recycled copper,” said Håkan Svensson, CEO of Dahrén. “Thanks to the long-term partnerships in our supply chain, we are able to secure a significant supply of this raw material and offer our customers the possibility to reduce their own carbon footprint, while retaining the high quality and performance of their products.”
ABB continues to bring increasing volumes of low-carbon and recycled copper into its production cycles while also committing to use more recycled electric steel (e-steel) and recycled aluminium. The aim is to reduce greenhouse gas (GHG) emissions while driving the transition to a low-carbon economy. ABB is increasingly designing its equipment to be recyclable, knowing that recycled copper, aluminium and steel offer energy savings of between 75 and 95 percent compared to virgin production.
“Through close collaboration with Dahrén and Boliden, ABB is helping to build a supply chain ecosystem with a low-carbon and ultimately a zero-carbon approach at its center,” said Ola Norén, Head of Metallurgy Products, Process Industries, ABB. “We are increasing our use of low-carbon and recycled copper winding wire in our EMS technologies all the time.”
ABB’s Metallurgy Products team has now ordered a stock of copper wire from Dahrén for use in the air-cooled EMS for aluminium applications, and the intention is to grow this to higher volumes in the future. The largest model has 2,200kg of copper wire per unit and the smallest 500kg of copper wire per unit.
Separately, ABB has a relationship with Finnish metals manufacturing specialist Luvata for hollow conductor wire made from Boliden’s certified recycled copper. The models of stirrers constructed using this stock of copper each have up to 2,700 kg of copper, saving up to 6,700 kg of CO2 per stirrer, based on verified industry-standard calculations.
EMS solutions deliver metallurgical improvements that are proven to increase productivity, end-product quality and reduce operating costs for electric arc, ladle and aluminium furnaces, as well as thick and thin slab and billet and bloom casters.
Source and Graphic: ABB