Application of low viscosity resin masses while producing electric motors
by Christiane Weiland
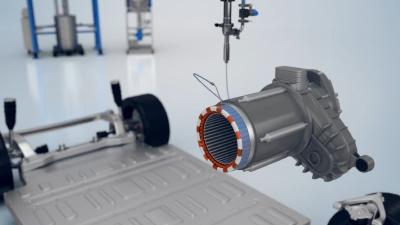
By trickling or impregnating the rotating drive components, the coils are provided with a protective layer. This process later improves the performance of the motors and generally extends their service life. After curing, the applied resin becomes a hard-elastic moulding material. It retains its good mechanical and electrical properties even at high temperatures. It insulates, prevents vibrations and the coils become more robust.
For the resin masses to harden, they - and also the stators - must be heated. This requires perfect process reliability. The components are either charged with electricity (electricity heat / induction) or heated in special industrial furnaces (circulating air heat) in so-called impregnation machines or trickle systems. The aim is a perfect trickle result and a precise flow of the resins between the windings of the coil.
ViscoTec dispensing systems are excellently suited for the application of resin masses and can easily be integrated into existing production lines.
The endless piston principle used in the ViscoTec dispensing pumps enables pulsation-free, continuous dispensing. Continuously adjustable in application quantity and application speed. Therefore, the dispensing technology specialist can guarantee an ideal penetration behaviour and a completely clean impregnation result, both when processing 1- and 2-component resin masses or trickle resins. ViscoTec dispensing pumps function regardless of viscosity. Even if viscosity fluctuations occur due to storage time or storage temperature, the dispensing functions perfectly. Dispensing is carried out from a dispensing tip with hose. A hardening of the pump is conceptually prevented.
The dispensing pumps are combined with the ViscoTec treating systems ViscoTreat-R or ViscoTreat-Inline. Thanks to optional vacuum suction, they ensure a completely air-free supply to the 1- and 2-component dispensers. The operator has no contact with the material.
Source and photo: ViscoTec