Dreeskornfeld invests in intelligent robot technology for deburring
by David Fleschen
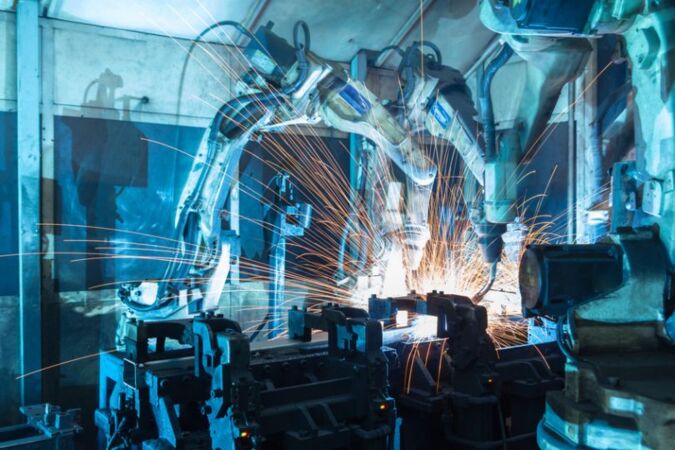
Loading and unloading deburring machines requires a high level of manpower, is time-consuming and physically demanding. Skilled labor is required for tasks with limited added value. For Dreeskornfeld, improved working conditions and cost savings were the main motivations for investing in Teqram EasyDebur robotization to automate the deburring process. This helps to combat the shortage of skilled workers and at the same time strengthens competitiveness.
Heinz Dreeskornfeld GmbH & Co. KG is a medium-sized company in the field of flexible sheet metal processing. At its site in Bielefeld, the company operates 11 flatbed lasers and 2 punch/laser combination machines. With a total workforce of 108 employees, 60-70 tons of sheet metal are processed daily. Production is mainly focused on the areas of agricultural & materials handling technology, vehicle construction, and mechanical and plant engineering.
Challenges in sheet metal deburring
At Dreeskornfeld, sheet metal blanks have been deburred by machines for a long time. As with 99% of sheet metal suppliers, the parts were previously placed manually on a conveyor belt and also removed manually behind the machine.
Due to the shortage of skilled workers, Dreeskornfeld was forced to look for an automated solution to expand its deburring capacity. Robotization offered itself as an obvious solution, but classic industrial robots require high quantities so that the programming effort per part is economical. In flexible sheet metal processing, however, such quantities are hard to find.
The robotic systems from Dutch automation specialist Teqram proved to be a suitable solution. Thanks to vision systems and AI-based control, Teqram robots can operate fully autonomously, completely without time-consuming programming or teaching.
After pressing the start button, the EasyDebur scans the pallets of parts in the receiving area. The EasyEye, in combination with 3D vision sensors in the gripper, recognizes pallets, stacks as well as the individual part geometries based on the scanned data. CAD data does not have to be transferred. The system autonomously decides which grippers are suitable for each part and changes them in automatically. In the background, the software also ensures that the number of gripper changes is minimized. The parts are then transferred to the input conveyor belt of the deburring machine. If there is a jam, for example due to a machine error, the loading process is automatically slowed down or stopped.
Source: Tegram, Photo: Fotolia