Primetals Technologies optimizes pickling line-tandemcold mill
by Hans Diederichs
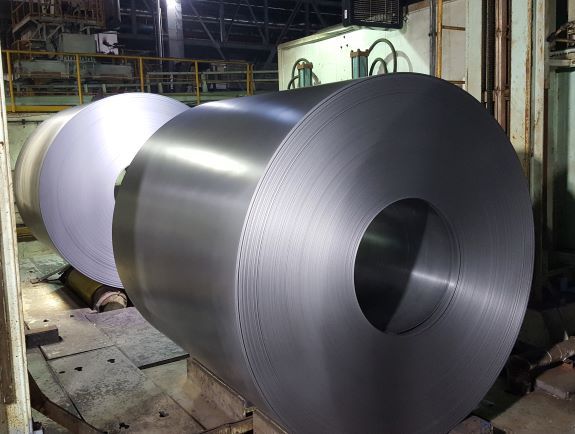
Primetals Technologies optimized the drive and automation equipment of the pickling line-tandem coldmill (PLTCM) no. 1 at the Dangjin plant of Hyundai Steel, a Korean steel producer, within a short periodof time. After a refurbishment phase at the end of 2018, all the agreed proofs of performance for theproduction of more than 20 different product groups were completed by January in a period of just fourweeks. The production capacity of the PLTCM was substantially increased at the same time, which nowenables it to supply cold-rolled strip to an additional strip galvanizing line at the Suncheon plant. Therefurbishment was preceded by a detailed analysis of the weak points of the entire plant and thedevelopment of a targeted refurbishment concept. This increased the production potential of the existinglines and minimized the investments needed for new equipment.The analysis preceding the refurbishment showed that, instead of replacing the entire drive train, onlythe drive trains on stands two and three had to be replaced to eliminate the weak points. The availableinstalled reserves of stands one, four and five were utilized and the load optimally redistributed toachieve the required increase in throughput for the complete plant. New transformers andcycloconverters were installed on stands two and three, and new motor and gear units were mounted onthe existing foundations. The "Motor Utilization Model – MUM" newly developed by PrimetalsTechnologies was used for the first time to make the maximum possible use of the installed performancereserves of the new and existing stand motors. The load was distributed optimally to adapt it specificallyto the product mix and to obtain the best possible dynamic use of the forming forces of the individual
Primetals Technologies, LimitedChiswick Park, Building 11, 566 Chiswick High RoadA joint venture of Siemens, Mitsubishi Heavy Industries and PartnersW4 5YS LondonCommunicationsUnited KingdomHead: Gerlinde DjumlijaReference number: PR2019041779enPage 2/3stands. The objective was to achieve the maximum degree of forming along the complete line, and tocome as near as possible to the load limits of the individual stands.The continuous power of the new machines is around 36 percent higher and they allow the rolling workto be optimally redistributed in the tandem mill. Some of the low-voltage drives were also replaced. Forexample, the rollers on the infeed side are now equipped with motors and drives that are up to50 percent larger in order to deliver the required pulling force at higher speeds. In addition to the renewalof the drive equipment, the technological controls in the basic automation and the Level 2 rollingregulations were modernized. The refurbishment of all parts of the plant was planned in great detail andcompleted right on schedule within the timeframe of 15 days. It was even possible to hold the first testsof the rolling operation one day earlier than scheduled. The first strip was successfully rolled as plannedon December 14, and the plant was brought up to its previous throughput within three days.All the verifications for more than 20 individual product groups – mainly interstitial free grades and otherproducts for the automotive sector – were completed by the end of the first month. The plant alsosignificantly surpassed the contractually agreed parameters within the first few weeks.PLTCM no.1 at Hyundai's Dangjin site now has a capacity of around 1.8 million metric tons per annum. Itprocesses cold steel strip in widths ranging from 600 to 1,800 millimeters. The entry thicknesses canvary between 1.2 and 6 millimeter, and from 0.25 to 3 millimeters on the exit side. The maximum stripspeed is 1,400 meters per minute. The line consists of four four-high stands and one six-high rollingstand. Primetals Technologies had equipped the line with process automation back in 2006.
Source: Primetals Technologies / Photo: fotolia