Salzgitter invests in new reheating furnace to improve energy efficiency
by David Fleschen
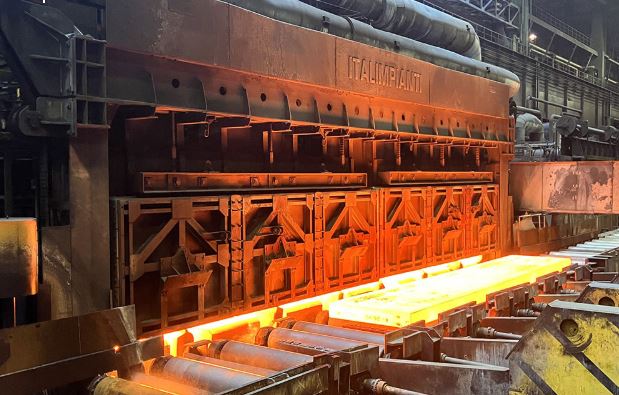
Salzgitter AG, through its subsidiary Salzgitter Flachstahl GmbH, has announced a significant investment in new energy-efficient infrastructure at its hot strip mill. The company is committing a three-digit million-euro sum to install a new walking beam furnace and an exhaust gas heat recovery system, aimed at reducing energy consumption and facilitating the future use of hydrogen.
The new walking beam furnace will be used to heat steel slabs—large blocks of cast steel—to temperatures of up to 1,300 degrees Celsius. These slabs serve as the base material for producing steel coils. Engineering firm Tenova Italimpianti has been contracted to deliver and install the furnace.
“With the new furnace, we will reduce our energy consumption for slab reheating in the hot strip division by up to 30%,” said Thomas Routschek, Operations Director for Hot Strip at Salzgitter Flachstahl GmbH. “This is another important step toward lowering the CO₂ footprint of our flat steel products. Once fully operational, all slabs at the Salzgitter site will be processed using walking beam furnaces.”
The combustion gases generated during the heating process will be captured and their residual heat converted into steam through a dedicated exhaust gas heat recovery system. DSD Power has been awarded the contract for constructing the heat recovery unit.
“The entire project is designed with energy efficiency in mind,” noted Felix Iwanowski from the Salzgitter Flachstahl hot rolling mill project management team. “The new system will make efficient use of combustion gases, and the high-quality steam generated will be distributed across the plant.”
Given the project’s emphasis on energy efficiency, it has qualified for funding from the German development bank KfW. Installation and commissioning of the new furnace are scheduled for completion by 2028.
Source and Photo: Salzgitter