SMS group: Environmentally friendly technology for the production of steel bars
by David Fleschen
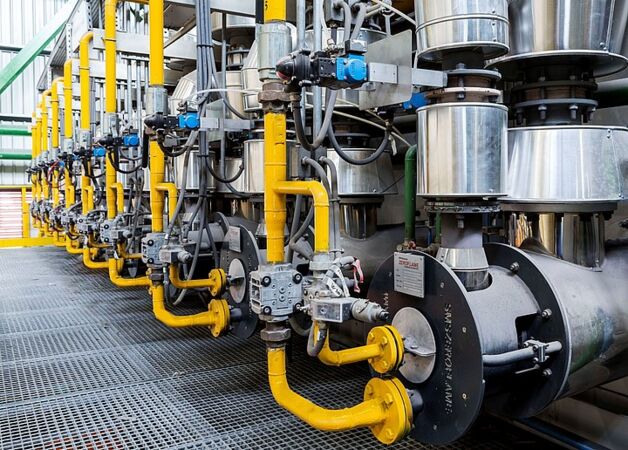
Megasider Zaragoza S.A.U., part of the Megasa Group since 2016, has placed an order with SMS group for the supply of a bar mill with environmentally friendly heating technology. The new plant will replace the existing rolling mill, which was also supplied by SMS in 2005. The plant is strategically located in the north-east of the Iberian Peninsula near Zaragoza, Spain, with excellent access to the major industrial regions of Spain and France. The plant will be designed to produce a wide range of bar products that will complement and expand the existing product portfolio.
SMS supports Megasider in its goal to realise a production operation without natural gas and to digitalise the plant. As a system supplier, SMS offers an overall concept for the operation of the flexible burners with a digital control system. This enables the plant to be operated in a particularly environmentally friendly way.
The SMS scope of supply includes a walking beam furnace equipped with the latest reheating technology for environmentally friendly operation. Specifically, the furnace with a capacity of 120 tonnes per hour will be equipped with the SMS Prometheus® Level 2 control system, which ensures uniform temperature distribution and low oxidation and carbon enrichment of the steel, as well as the SMS DigiMod combustion management system and SMS ZeroFlame HY2 burners. These ultra-low NOx flameless burners can run on both natural gas and a mixture of natural gas and hydrogen in any ratio, allowing complete conversion to hydrogen operation. The combination of SMS ZeroFlame HY2 burners, DigiMod combustion management system and SMS Prometheus® control system reduces NOx emissions to 45 ppm, scaling to 0.4 per cent and fuel consumption to 27 Nm3 per tonne.
The scope of supply also includes a multi-strand straightener with automatic bar positioning and feeding and an automatic roll changing system, a cold saw for use with grinding or metal discs, and an automatic magnetic stacker with rotating arms that has four independently operating four-metre sections. The high-precision profile measuring device with surface defect detection, supplied by TBK, a company of the SMS group, enables Megasider to carry out non-contact precision measurements for optimum processes in bar production.
The entire plant is controlled by the X-Pact® automation system, the Level 1 and Level 2 solution from SMS group. This holistic approach aims to transfer SMS' many years of experience in the field of automation to the rolling process in order to maximise the performance of the plant. At the same time, it enables the immediate implementation of digital solutions based on harmonised data processing.
"We are proud that Megasider has put its trust in SMS' pioneering technology and that we are able to supply a new plant that sets standards in the environmentally friendly production of bar," says Luigi Barbante, Vice President Bar & Wire Rod Mills at SMS group.
Source and Photo: SMS Group